CNC MACHINE GUIDE: TYPES, USES, PRICES, DEFINITION
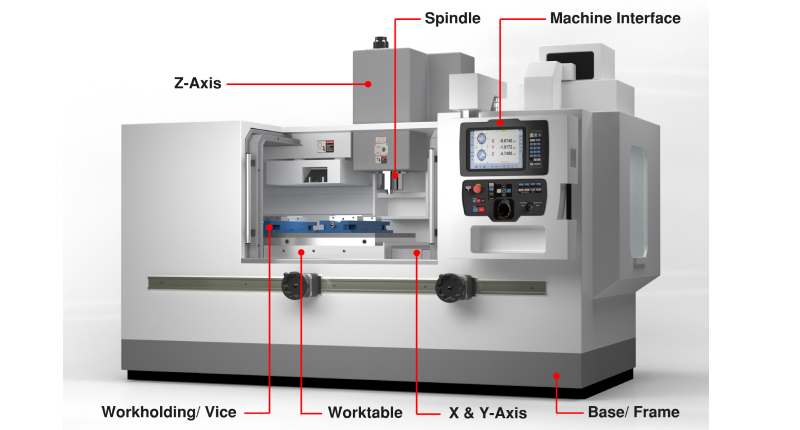
CNC machines play a pivotal role in contemporary manufacturing across diverse sectors, a far cry from the era when manual machines dominated the production landscape. In the past, each milling machine, lathe, and grinder typically necessitated a skilled machinist to operate, rendering machining processes labor-intensive.
In the present day, the manufacturing industry thrives on automation and efficiency. Modern machine tools boast advanced control systems, empowering companies to manufacture parts of superior quality with unprecedented precision.
This guide delves into the various types of CNC machines, such as lathe machines, routers, milling machines, grinders, and more. We explore their functionalities, examine how manufacturers leverage them, and provide insights for potential buyers, including considerations on the cost of these CNC machines.
What does CNC mean?
CNC stands for computer numerical control, representing a sophisticated manufacturing process that employs software to oversee the operations of various CNC machines. Simply put, a CNC machine refers to any machine integrated with CNC technology and functionalities.
This technology enables machinists and skilled professionals to utilize mechanical design, drawings, mathematics, and computer programming expertise to fabricate precise parts. With CNC programming and operation, a metal workpiece can be transformed into a crucial component for aerospace or automotive applications with unparalleled accuracy. Contemporary machines often consolidate multiple tools into one, enhancing the efficiency of the CNC machining process.
What does a CNC machine do?
The main purpose of CNC is to manage the movements of a machine tool. Digitized data, a computer, and a computer-aided manufacturing (CAM) program collaborate to oversee, automate, and supervise the actions of the CNC tools. In extensive industrial machines, an integrated computer serves as a dedicated onboard controller, whereas smaller hobbyist models rely on an external computer.
Every CNC controller collaborates with multiple motors and drive components to carry out and regulate the programmed motions. In advanced machines, a feedback system consistently monitors and fine-tunes the cutter’s speed, feed rate, and position.
What is an example of a CNC machine tool?
The milling machine stands out as perhaps the most widely recognized example of a CNC machine tool. However, numerous others exist, including lathes, electric discharge machines (EDM), grinders, laser cutters, plasma cutters, waterjet cutters, CNC routers, and 3D printers. While the CNC machining process may differ to some extent for each of these, the fundamental principles of the machining process remain consistent across all.
CNC machines are also available in various sizes, ranging from compact desktop CNC machines like tabletop mills or benchtop routers to robust, large horizontal machining centers. Let’s delve into each of these machines individually to explore their distinctive features.
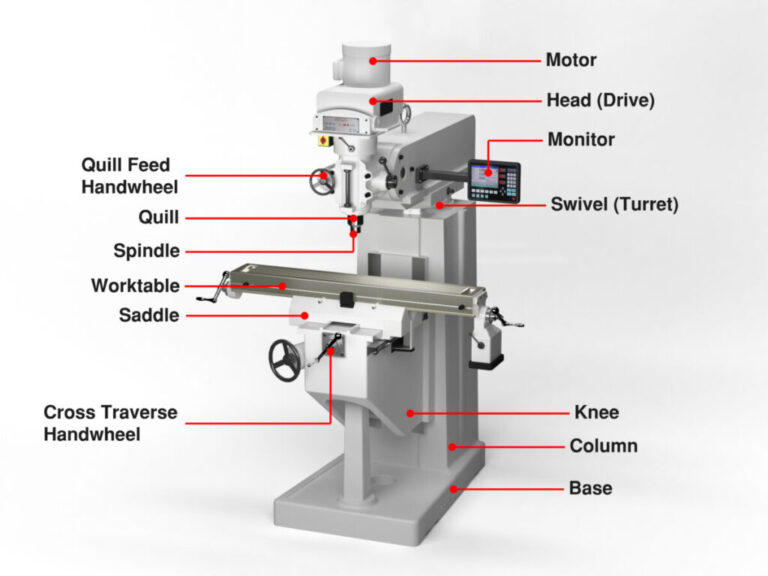
How does a CNC milling machine work?
The CNC milling process initiates by creating a part using computer-aided design (CAD) software, followed by converting it into a format compatible with the CNC mill. Computer-aided manufacturing (CAM) software then translates the design into a CNC machine program, usually in G-code format. The machine interprets these coded instructions and executes them, guiding every movement to replicate the CAD design accurately in the designated material. CNC machines provide advantages such as high production output, decreased labor costs, and consistent repeatability.
What are the uses of a CNC milling machine?
A key advantage of CNC milling lies in its versatility. CNC mills excel at cutting a variety of materials such as steel, iron, aluminum, composites, alloys, and more, enabling the rapid production of custom-designed parts compared to traditional machining methods. They can operate in both vertical and horizontal positions, mill flat or at an angle, and craft irregular surfaces or cavities.
CNC machines prove particularly effective in mold work, where precise control of two or three axes on the milling table is essential for generating cavities and intricate surface contours. These machine tools are well-suited for producing a wide range of items, from cast iron foundry patterns and core boxes to intricate stainless steel components used in aerospace, military, and medical applications.
What should you consider when purchasing a CNC mill?
Considerations:
Size Specifications: Align the dimensions of the CNC mill with the specific tasks you intend to perform.
Brand Reputation: Opt for top CNC milling machine brands known for their excellent track record.
Programming User-Friendliness: Since each machine tool varies, ensure the selected one allows easy program creation.
Footprint Size: Check the machine’s dimensions to confirm it fits within the available space.
Service Support: Ensure the manufacturer offers accessible and cost-effective support when needed.
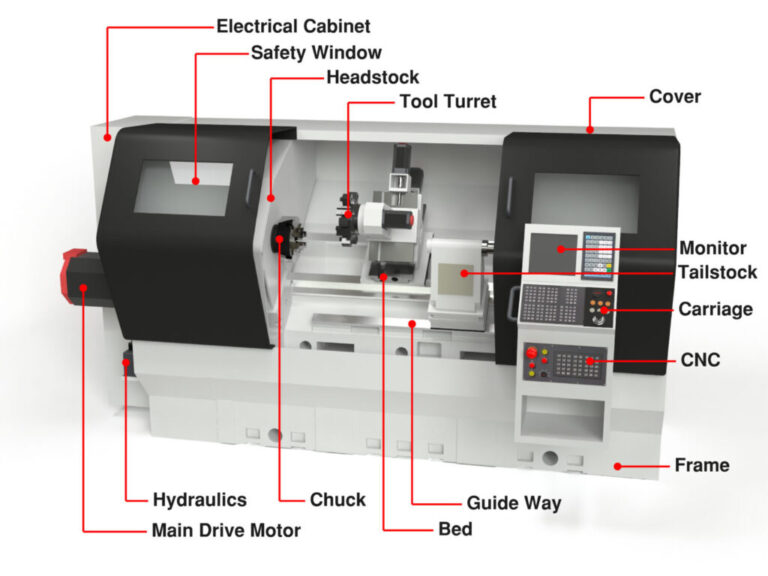
CNC Lathe Machine
How does a CNC lathe machine work?
Similar to the CNC mill, the CNC lathe necessitates a computer-aided design (CAD drawing) that can be transformed into a computer-aided manufacturing (CAM) format. This design is then exported to a CNC machine program featuring a tool path in G-code format.
In the CNC lathe process, the workpiece is secured between two centers, within a lathe chuck, or a collet. As the spindle rotates, the cutting tool engages with the material, shaping round parts and creating drilled or bored holes. In contrast to manual lathes, CNC lathes are capable of handling intricate tasks of various sizes and typically require a skilled operator with comprehensive training.
What are some common uses of a CNC lathe machine?
CNC lathes are equipped with a rotating spindle and a stationary tool, enabling the production of cylindrical parts used in a variety of products across the metalworking and woodworking industries. This versatility makes them nearly as adaptable as CNC mills.
Functioning as efficient production machine tools, many CNC lathe machines have the capacity to manufacture thousands of machined parts in a single shift. Smaller machines are designed for handling lesser quantities and are suitable for maintenance and jobbing shops.
CNC lathe machines exhibit the ability to remove material rapidly for parts that do not necessitate a smooth finish or slowly for cases where detailed features require a fine finish. They find applications in diverse industries, including automotive, aerospace, firearms, and electronics.
Here are some specific examples of parts crafted using CNC lathes:
Camshafts
Screws
Crankshafts
Baseball bats
Table and chair legs
Gun Barrels
Musical instruments.
What should you know before deciding on a CNC lathe?
- What kinds of parts and materials will you be producing?
- How many axes will you need for these parts?
- Is the CNC lathe compatible with your existing CAM software?
- Will the machine fit in your shop?
- Will the parts fit on your CNC lathe (both length and diameter)?
- Will the manufacturer provide affordable service and support when you need it?
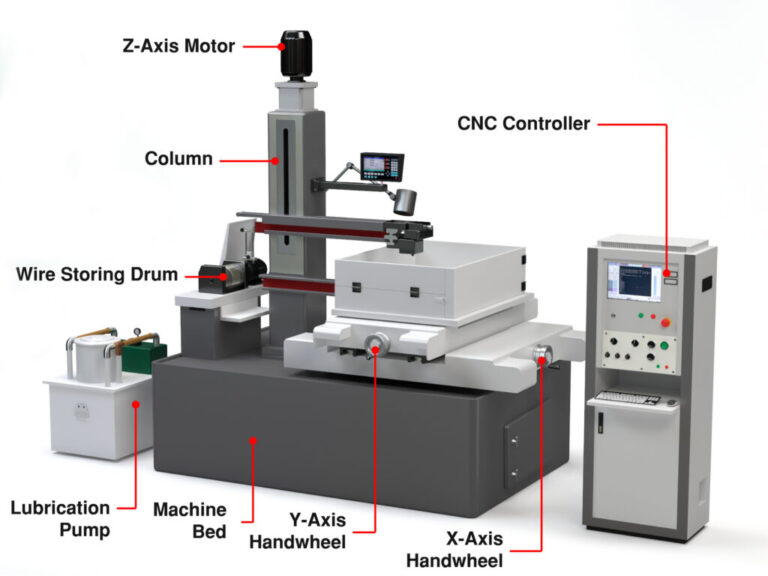
CNC Wire Electric Discharge Machine (EDM)
How does A wire EDM work?
Wire EDM is a manufacturing process that uses a thin brass or copper wire to cut hardened workpieces. The wire acts as the electrode, and the material is removed from the workpiece by frequent current discharges between two electrodes (the wire and the workpiece). The electrodes are separated by a dielectric fluid (typically deionized water) and subjected to electric voltage. The wire continuously unwinds from a spool.
What are some common uses of wire EDM?
Wire EDM is frequently used in the mold and die manufacturing processes, primarily for extrusion dies and blanking punches. EDM works well for both prototypes and total production runs and is most effective for manufacturing metal components and tools. The automotive, aerospace, and electronics industries often use EDM for their parts.
What should you consider when purchasing A wire EDM?
After the initial expense, the two most critical factors to consider are the ongoing expenses of consumables and maintenance. In other words, how quickly will this EDM get your parts off the machine using the least amount of wire, and how much downtime will you sustain from maintenance and repair? These factors are hard to quantify unless you have EDM experience, so your best bet is thorough research and talking to a few manufacturers with wire EDM knowledge.
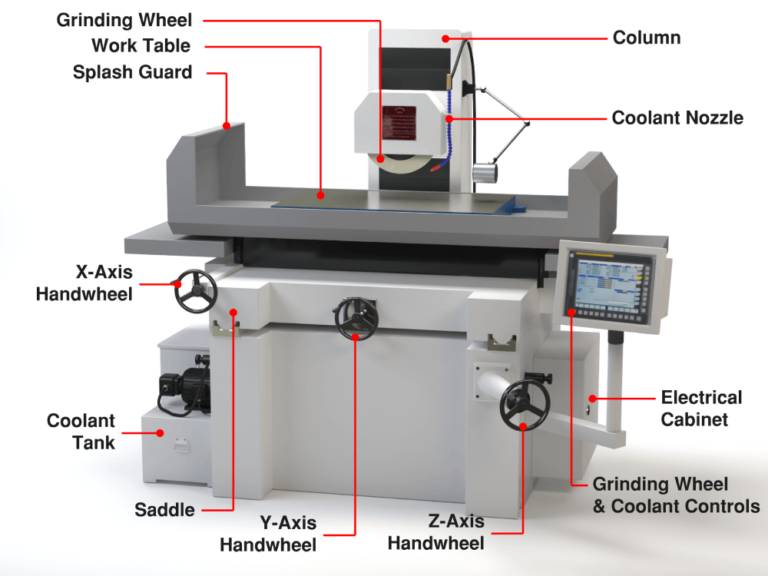
CNC Grinders
How does a CNC grinder operate?
CNC grinding machines are precision machine tools utilizing a high-speed rotating grinding wheel to eliminate metal from a workpiece. Programmed to enhance surface finishes and uphold specified tolerances, a CNC grinder automates the process.
While various types of CNC grinders exist, the surface grinder and the cylindrical grinder are the most commonly used. CNC surface grinders function automatically, following a programmed routine to achieve the finest finish on flat surfaces. On the other hand, cylindrical grinders work on round workpieces, grinding the outside diameter (OD) or inside diameter (ID) to exact specifications.
What are the typical applications of grinders?
Grinding finds widespread use across industries and various applications, including:
Whenever a precise surface finish is crucial.
Grinding various tools and cutters.
Achieving precise internal grinding on tapered, straight, and formed diameters.
Conducting cylindrical grinding on external diameters, such as shafts, pistons, camshafts, etc.
Performing slitting and parting operations.
What factors should be considered when buying a grinder?
To make an informed purchase, first, identify the type of grinder required based on the nature of the work (flat or cylindrical). Then, take into account the grinder’s specifications:
Grinding wheel diameter and speed.
Machine horsepower.
Frequency and volt rating.
Input power needed for various operations.
The material to be ground.
Presence of a coolant system.
CNC Laser Cutters
How does a CNC laser cutter function?
CNC laser cutting is a contactless thermal machining process that directs a high-intensity laser beam onto a metal workpiece, melting and cutting it to achieve the desired shape. This operation involves a CNC laser cutter equipped with a laser head containing a focusing lens and a nozzle. The nozzle emits a laser beam while allowing compressed gas flow, which cools the focusing lens and removes vaporized metal from the workpiece.
The point where the beam meets the workpiece reaches an extremely high temperature, leading to the vaporization of the metal. CNC programming and technology control the movements of the laser head and beam on the work surface, enabling the formation of custom shapes and designs.
What are the common applications of laser cutters?
Laser cutting machines are invaluable for engineering applications, especially when precision cutting of machine components is crucial. These cutters are also used for cutting structural and piping materials, as well as flat sheet metal. CNC technology facilitates easy adjustments, allowing for etching or engraving various designs on metal, wood, and plastic. The capabilities of the laser cutter, determined by its size and capacity, dictate the type of work it can handle.
What factors should be considered when buying a laser cutter?
Three main types of laser cutters are available:
CO2 Laser Cutters: Efficient and cost-effective, these cutters are popular for their ability to cut materials like glass, plastics, leather, wood, and acrylic.
Crystal Laser Cutters: Featuring smaller wavelengths and higher intensity compared to CO2 lasers, crystal laser cutters can cut through thicker materials, including metals, plastics, and ceramics.
Fiber Laser Cutters: Also known as solid-state lasers, fiber laser cutters excel in cutting reflective and conductive metals. They boast three times the efficiency of CO2 cutters, require less maintenance due to having no moving parts, and are suitable for metals and organic materials.
CNC Plasma Cutters
How does a plasma cutter operate?
CNC plasma cutters are automated machines controlled by a computer that guides a high-definition plasma torch based on numerical coding (G-code) programmed into the system. The plasma cutter functions by propelling a gas or compressed air through a nozzle at high velocities and subsequently introducing an electric arc to the gas, generating plasma capable of cutting through metal.
Various gases are utilized in plasma cutting, including:
Oxygen: Employed for cutting mild steel up to 1-1/4 inches thick.
Argon and hydrogen mix: Delivers high-quality, smooth cuts in stainless steel and aluminum.
Compressed air: Suitable for low-current cutting applications in metals up to 1-inch thick.
Nitrogen and methane: Effective for thin stainless steel.
What are the common applications of plasma cutters?
Plasma cutters find application in fabrication shops, automotive repair and restoration, construction, and salvage operations. Artists and designers utilize them for crafting signage, sculptures, and decorative panels for various interior projects.
Primarily, plasma cutters are used for cutting steel, brass, copper, and other conductive metals, though they are less effective on stainless steel and aluminum. They excel in cutting larger parts with loose tolerances, making them ideal for general plate cutting due to their quick cutting speed and cost-effectiveness compared to other cutting methods.
What factors should be considered when buying a plasma cutter?
Since plasma cutters can handle virtually any type of metal, the primary consideration lies in metal thickness and the anticipated cutting volume. Consider the following questions as you match a plasma cutter to your specific needs:
Are you cutting thick metal?
How frequently will you use the plasma cutter?
Will you need to modify power outlets for the new cutter?
Do you have an existing generator for use with the plasma cutter?
Will there be fluctuations in your electrical current?
Is portability a crucial requirement for your unit?
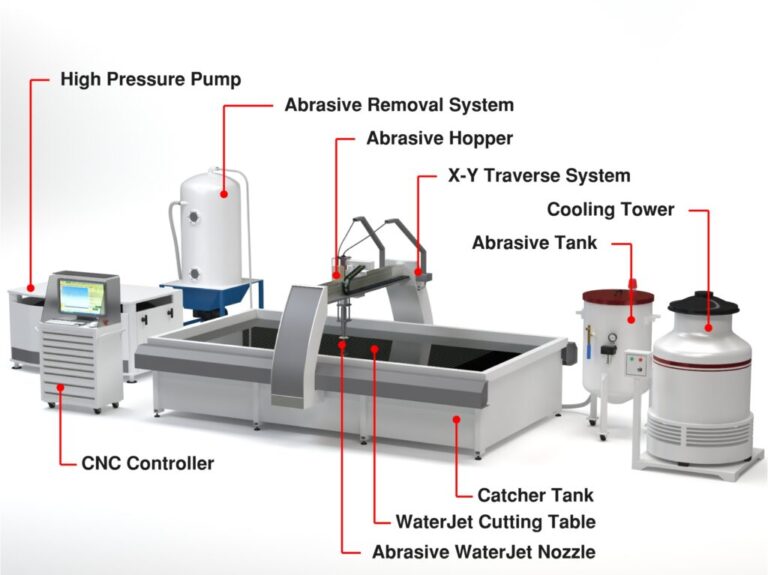
CNC Waterjets
How does a waterjet function?
Waterjet cutters are precision machine tools utilizing a high-pressure stream of water to create an ultra-thin cut on a workpiece. Occasionally, a granular abrasive is introduced to enhance cutting power, easily adjustable at the nozzle for transitions between water-only and abrasive cutting.
Waterjet cutters operate by directing pressurized water through a ruby or diamond nozzle into a mixing chamber. This process creates a vacuum, drawing garnet sand into the stream, which is then propelled at the material. The jet stream moves at speeds up to 2.5 times the speed of sound, enabling efficient and powerful precision cutting.
What are the typical applications of waterjets?
Waterjets find extensive use in various glass projects, including kitchen splashbacks, stained glass, shower screens, and floor inlays. Other applications encompass:
Metals like steel, aluminum, titanium, brass, and nickel.
Stone and marble, for decorative wall and floor tiles, stepping stones, and countertops in kitchens and vanities.
Soft materials such as foam, interior automotive components, rubber, plastic, and cork.
Metal parts for the automotive industry, including bumpers, truck bed liners, fiberglass body parts, and trim.
Aerospace industry components like engine parts, cabin panels, and aluminum body parts.
The electronics industry uses waterjets for crafting circuit boards and various other parts.
What factors should be considered when buying a waterjet?
Size: Ensure the waterjet’s size can accommodate your parts, the supplied sheets, and potential future growth. Machines with dimensions like 5’ X 10’ or 6’ X 12’ typically work well.
Ongoing Costs: Consider both initial and operational costs, where the expense of abrasive recycling systems should be weighed against the benefits of using fresh abrasive.
Pump Pressure: While an Ultra High-Pressure Pump is not always necessary, a higher HP option with a proven track record may suffice, offering cost savings.
Used Components: For those seeking an abrasive removal system, explore aftermarket options before committing to an expensive in-tank dedicated system.
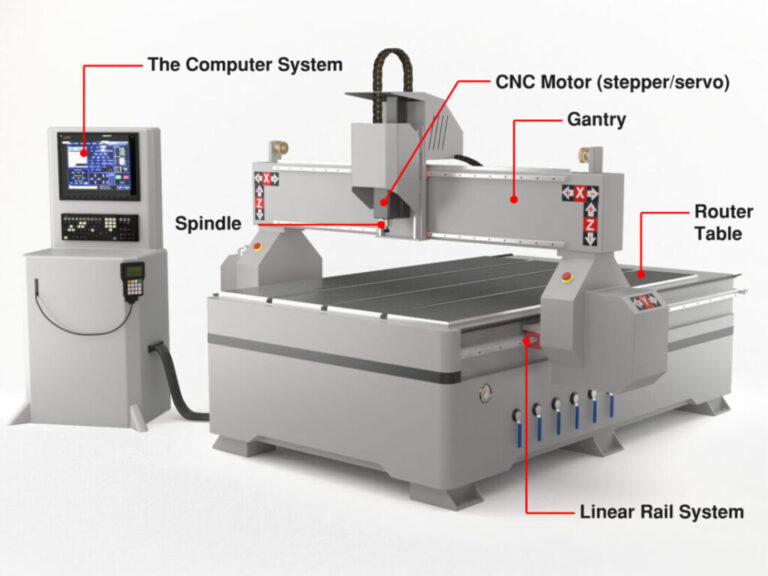
CNC Routers
How does a CNC router function? Similar to other CNC machine tools, CNC routers utilize CAM software programs and G-code to govern the machine’s movements, timing, and direction. Equipped with spindles holding cutting tools, CNC routers create shapes in various materials on a work table. These cutting tools can perform tasks such as drilling holes, milling cavities, engraving, and more.
Operating akin to a milling machine, the CNC router’s drive system directs the spindle along the X, Y, and Z axes, enabling the machining of intricate patterns and contours. While sharing similarities with mills, CNC routers are less robust and are better suited for cutting softer materials like wood.
What are the common applications of routers?
CNC routers find widespread use in various applications, including:
- Furniture making: Capable of producing diverse furniture items in large quantities.
- Sign making: Renowned for their versatility, CNC routers are excellent for crafting signs.
- Cabinet making: Suitable for creating shelves, drawer fronts, side panels, and custom doors.
- Arts and crafts: Useful for crafting items like picture frames, CNC Christmas projects, and plaques.
- Molds and prototyping: Ideal for machining 3D design models in epoxy, foam, and clay, as well as cutting molds from materials like EPS foam, polyurethane foam, EVA foam, and plastic.
What factors should be considered when purchasing a CNC router?
- Type of drive system: Choose between rack and pinion, lead screw, and ball screw. While ball screws are more expensive, they enable cutting larger workpieces with enhanced accuracy and efficiency.
- Servo vs stepper motors: Stepper motors, with more magnetic poles, offer improved accuracy, while servo motors provide twice their rated torque for specific periods and generally exhibit greater efficiency.
- Machine weight: Heavier machines are generally more robust, resulting in less vibration and more precise cutting.
- Software: Invest in quality software, as the CNC router’s performance is dictated by the instructions it receives from the software.
3D Printers
The preceding eight machines operate using a subtractive manufacturing process, meaning they remove material through various methods. In contrast, 3D printers employ an additive manufacturing process to create three-dimensional solid objects from digital files.
In this additive approach, each part is formed by depositing successive layers of material, with each layer representing a thinly sliced cross-section of the object. 3D printing stands as the antithesis of subtractive manufacturing, constituting a unique and relatively recent process that continues to undergo advancements. Given its distinctive nature, 3D printing warrants a comprehensive examination, though we will only touch upon it briefly for now.
Two Examples of High-Quality CNC Machines
While modern computers form the core of every CNC machine, superior engineering sets the exceptional ones apart from the rest. The CNC Masters Supra Vertical Knee Mill and their 1440 CNC Lathe Machine exemplify excellence. Both CNC machines are manufactured in the USA (Irwindale, California) and come with dedicated support teams.
CNC Supra Vertical Knee Mills
Offered in two table sizes, the Supra stands as a Bridgeport-type CNC knee mill with numerous beneficial features, all at a price point that makes it accessible to small shops and hobbyists. This versatile CNC milling machine is well-suited for production work, product development, rapid prototyping, engraving, and educational applications in community colleges, vocational schools, and science labs. Its user-friendly controls and software enable quick proficiency, allowing users to create both simple and complex parts efficiently.
1440 CNC Lathe Machine
Put an end to outsourcing high-volume round work and the associated exorbitant costs. The 1440 CNC Lathe transforms intricate manual turning applications into easily programmable tasks, ensuring accurate production runs for complicated parts. Additionally, when dealing with single-piece runs, the 1440 CNC Lathe swiftly and efficiently reverts to manual control, eliminating the need to develop a CNC program for short runs.
Consult with the CNC Lathe and Milling Machine Experts.